Strong in
customized
solutions
and product development.
Klik op de bewerken-knop om deze tekst te wijzigen. Lorem ipsum dolor sit amet.
screen
In sieving technology, the need for the right screen is often underestimated.
A poorly tensioned screen directly affects the capacity AND efficiency of your vibratory separator.
AMKCO has been supplying screens for different types of vibratory separators for many years. Often for a round machine but always a screen that is produced according to the highest quality requirements.
A vibratory separator vibrates a screen and ensures that the product is sieved to the correct size. When a screen is poorly tensioned or even has no tension at all, the product will not only be sieved less well, but the product will also not move on the screen. Product that does not move will not leave the vibratory separator or leave it badly, resulting in the screen filling up and the capacity and efficiency of the machine deteriorating.
AMKCO supplies mounted pre-tensioned screens, which means that the sieve mesh is glued or clamped under tension on a ring or frame. This is done under ideal conditions, which always guarantees the highest quality so that you have a screen that meets the highest requirements and has the longest possible service life.
Each sieve mesh used by AMKCO complies with the quality standard as defined in DIN ISO 9044
In addition to manufacturing new screens, AMKCO also supplies re-screens for many other types of vibratory separators. Round or rectangular is of secondary importance. If you have the ring or frame, AMKCO can provide it with a new pre tensioned sieve mesh.
Types of sieve mesh
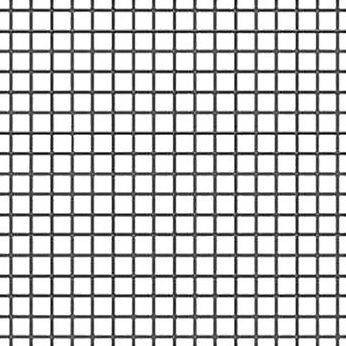
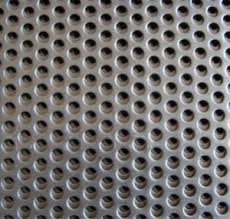
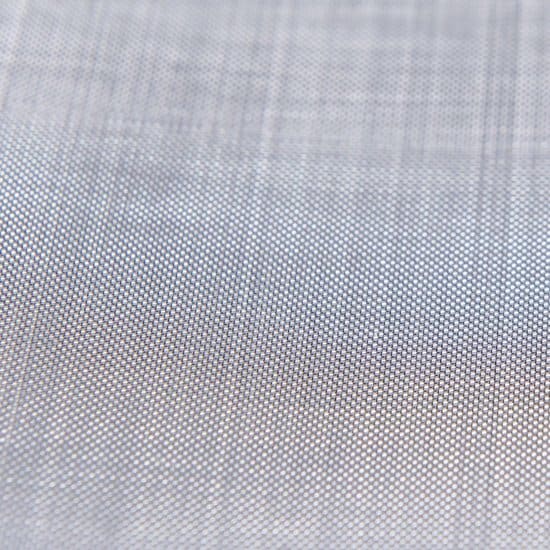
AMKCO supplies different types of sieve mesh. The choice of the material, opening, and wire thickness is often decisive.
Sieve mesh is usually available in stainless steel 304 or stainless steel 316. AMKCO preferably stock all screen cloth in stainless steel 316. However, some processes require different qualities. For example, sieve mesh is available that is magnetically traceable (stainless steel 430 or even Duplex). AMKCO has an extensive network of screen mesh suppliers with which almost any question can be filled.
In addition to the choice of material, there is also a wide range of sieve meshes available with different wire thicknesses. The choice of a certain wire thickness affects the life of a screen on the one hand, but the capacity of the machine on the other. Sieve mesh with a thinner wire has a higher percentage of “open area” and therefore a larger passage. For example, a larger capacity can be achieved within the same machine by simply selecting a screen mesh with the same opening and a thinner wire. Of course, the thickness of the wire directly affects the life of a screen. That is why it is always wise to work with an AMKCO specialist to see which type of sieve mesh is most suitable for your application.
Custom made from fine to coarse sieve mesh.
Screen specials
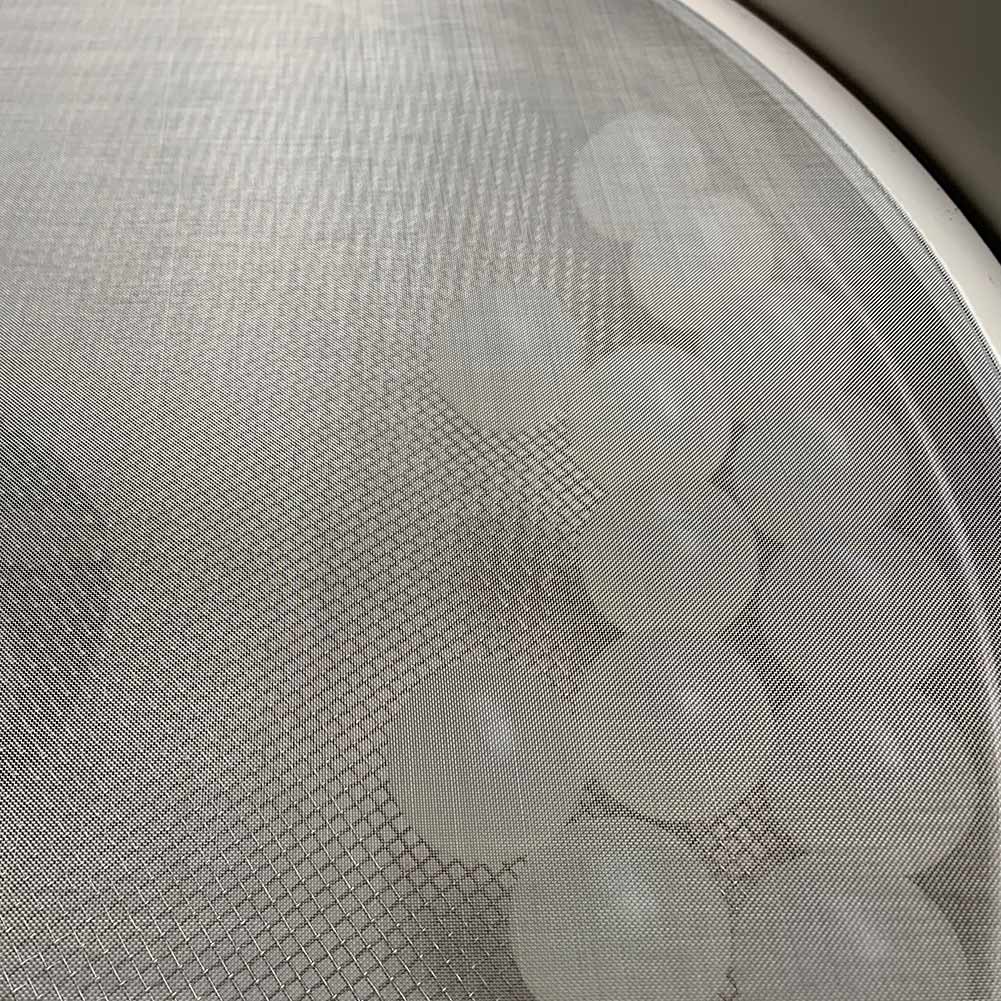
Screen decks Special AMKCO Europe
Ball cleaning is a mechanical cleaning that is usually applied in dry applications and a mesh size of 1 mm and larger. The impact of balls is high but the hitting area of balls is relatively small. Cleaning coarse screen mesh (larger than 1 mm) requires a lot of impact and is less dependent on the contact surface.
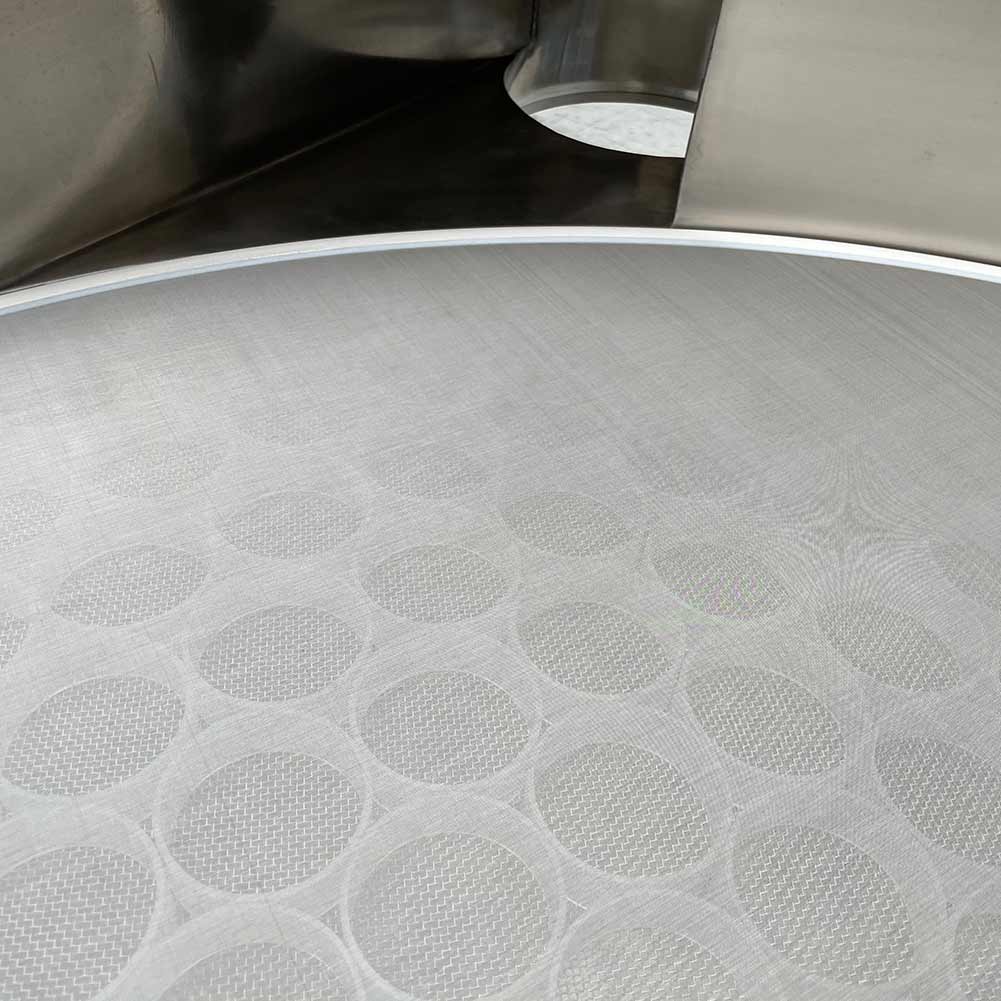
Screen decks Special AMKCO Europe
Ring cleaning is also a mechanical cleaning and is used in both dry and liquid applications. The rule of thumb is that rings are used with screen mesh up to a size of 1 mm. The impact of rings is low but the contact area of rings is very large because there is a full package of rings under the screen mesh. The screen mesh is continuously and intensively cleaned on the vertical vibration of the machine.
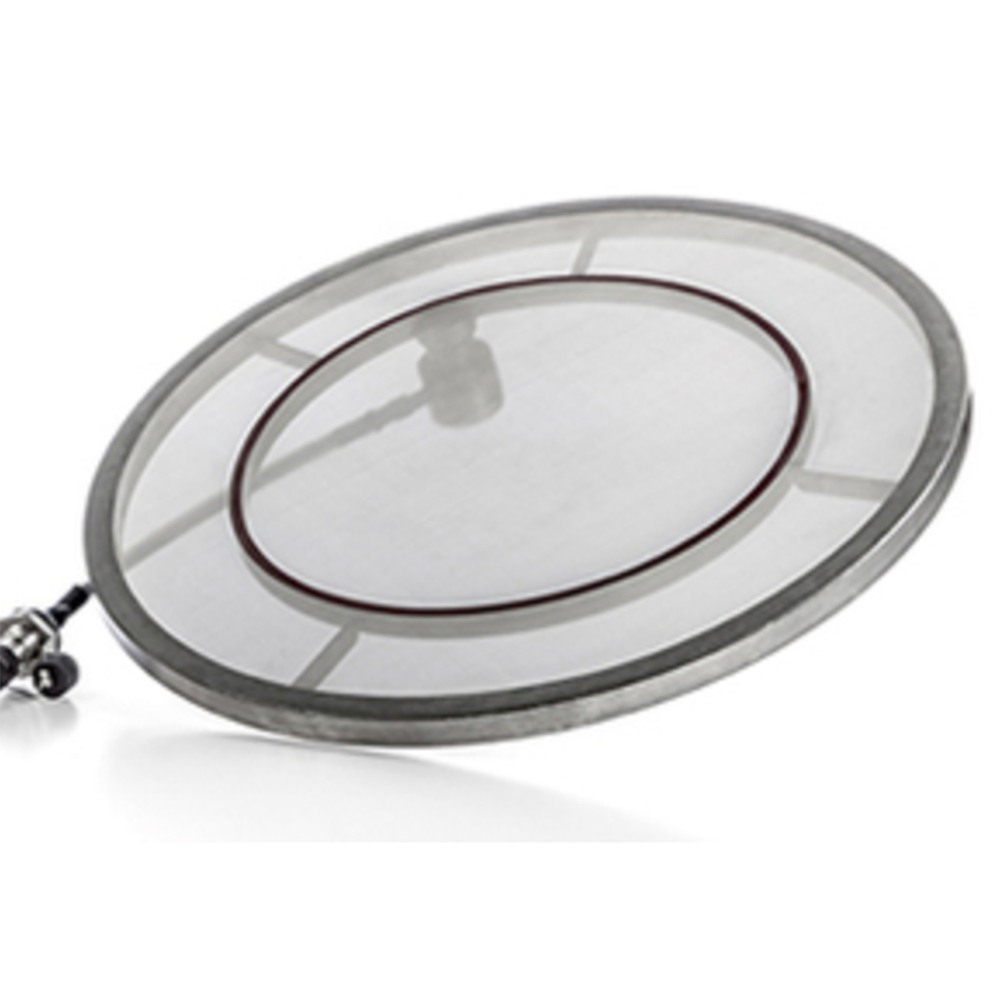
Screen decks Special AMKCO Europe
Ultrasonic cleaning is an external cleaning in which an installation generates a vibration of 37 kHz, which is emitted to the screen mesh. Ultrasonics are mainly used for very fine powders and very fine screen mesh.
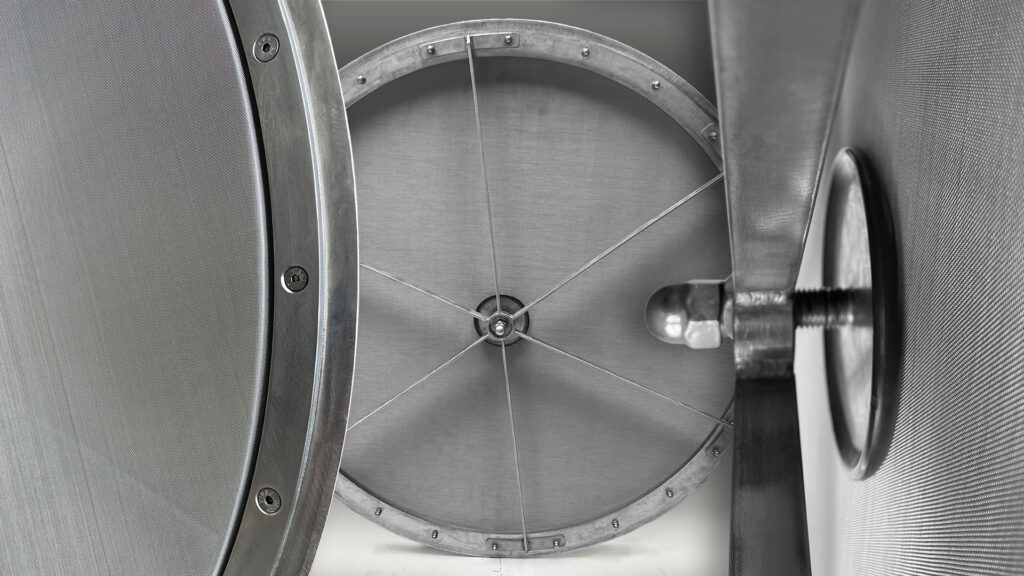
Customization is what we are strong at
We produce all screens in our screen production hall and can therefore produce screens for all brands and in any desired shape.
Of the competing brands, we also have the desired frames in stock, so the delivery time can be short.
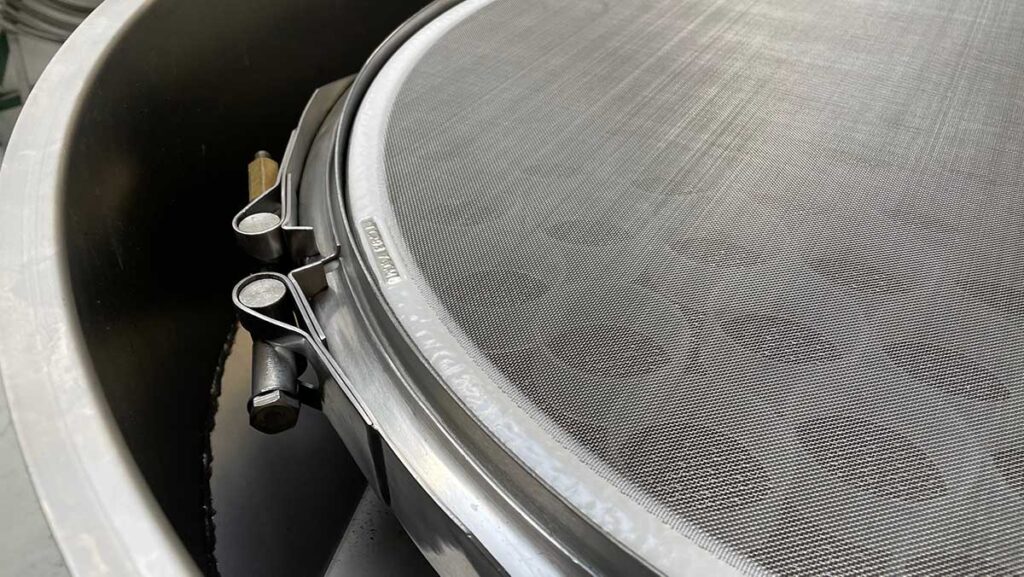
Raised overflow edge
This application is used when the product to be sieved has to stay on the sieve longer for the desired sieve result. The self-cleaning screen Is kept clean by means of sliders.
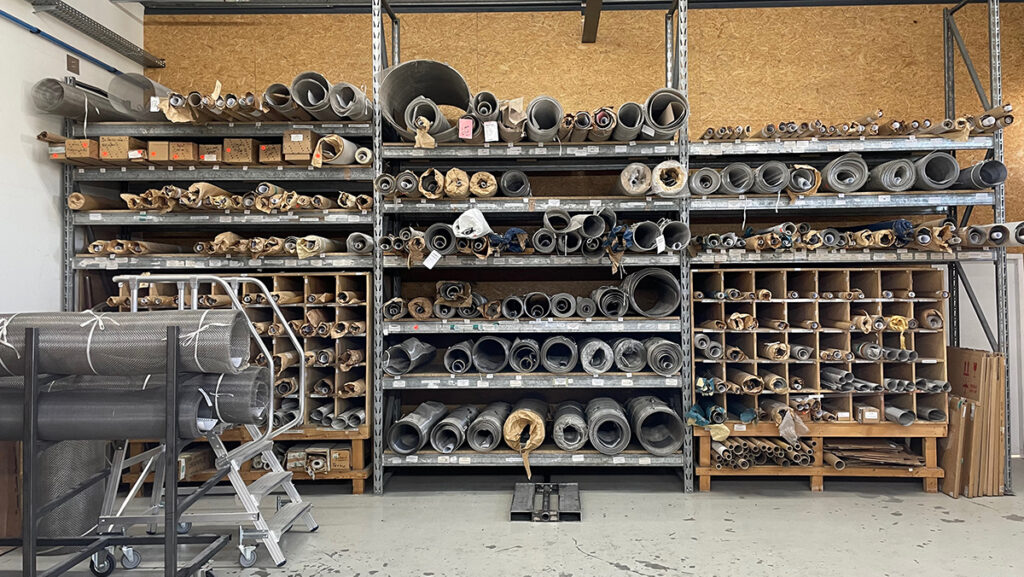
Sieve mesh stock
AMKCO Europe maintains an inventory of screen cloth mesh for almost all applications. Service contracts and special arrangements with customers assures a steady supply of screens of the correct size and mesh are always available. Many products to be sieved are tested in the special test room or on location. Due to these conditions and the use of high-quality sieve mesh, the AMKCO mounted screen has quality and provides maximum service life. The screens are also suitable for many competing brands such as Russel and SWECO
Process from right to round
Process 1
Rolling the profiles
Process 2
Welding the profiles
Process 3
Selection of the sieve mesh
Process 4
Tensioning the sieve mesh
Process 5
Gluing the sieve mesh
Process 6
Screen ready for our customer
Working with AMKCO Europe is
Reliable
Service-oriented
Tailor-made solutions
Flexible
Efficient
Fast delivery
Reliable
Service-oriented
Tailor-made solutions
Flexible
Efficient
Fast delivery
Please contact the specialist in sieving solutions without obligation
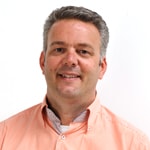
Our goal is to improve your production process together.
Direct contact
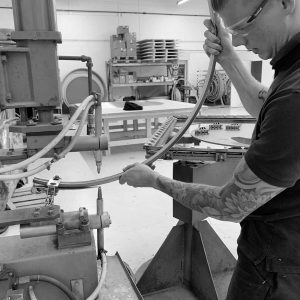